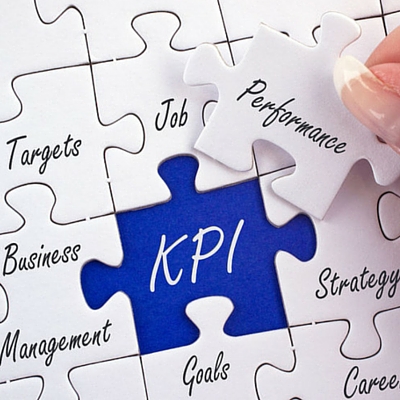
KPIs measure the performance of business processes against pre-established standards
What are KPI for Bakeries?
Key Performance Indicators (KPIs) measure the business performance of various bakery business processes throughout a bakery’s manufacturing scope and supply chain. It supports the wise old saying “You can’t measure what you can’t see” or “You can’t fix what you can’t see”. KPIs are business health performance measures. It is no different than getting an annual physical from your doctor. He or she will conduct a blood analysis, a heart analysis, and measure your pulse. Just like we individually need a hear doctor, so we need a business doctor who can analyze the health of our bakery.
As business processes define a business organization, KPIs measure the performance of business processes against pre-established standards. KPI performance data becomes truly valuable to executives and managers when it is reported to them on a real-time continuous basis instead of weekly or biweekly reports. Achievement of real-time reporting can only happen when information technology solutions are completely integrated and aligned with established business processes.
Traditional KPI Management Shortfalls
Traditional KPI management the food industry has focused on a bottom-up approach with specific KPI measurements at “operations islands” or “silos” within an organization. Roddy Martin, AMR Research, stated that locally driven bottom-up manufacturing KPIs, such as quality, throughput, and cost, often conflict with top-down strategic business goals such as customer service and market share. Local department improvement does not always translate to overall business improvement. KPIs must provide the means for manufacturing to align, monitor, and sustain performance by driving practices that improve overall business performance geared toward better customer service, etc. For example, schedule adherence on the shop floor improves planning and fulfillment performance in the supply chain.
Benefits of New Top-Down KPI Management in Bakeries
Organizations benefit most through top-down KPI management when they integrate goals and KPI measurements across departments throughout their enterprise. To that end, AMR Research has identified the following business practices help optimize organizational benefits:
How to align, prioritize and co-ordinate KPIs and business goals:
- KPIs must be carefully applied to those processes that support the enterprise business drivers and performance metrics
- A detailed, cross-functional analysis of business processes, rules, specifications, process events, and triggers must define measurements required to track a KPI
- KPIs must be coordinated and conceptualized across all manufacturing plants
- Credible, influential, and IT savvy domain specialists must perform KPI analysis and systems integration (That’s the Bakery Solutions Business Model)
- Avoid introducing point solutions throughout an enterprise
- Users must influence the strategic direction of vendor product strategies and KPI developments so that KPI scope and capability can be aligned with specific business priorities.
KPI Examples for Millers and Bakers
To better understand what some bakery business KPIs are, I have listed a few in various aspects of milling and baking operations:
Examples of Enterprise of Corporate Bakery Business Drivers:
- Measure of Market Innovator
- Increase Corporate Profit Margins X%
- Target Lowest Industry Operating Costs
- Increase Shareholder Value 25%
- Highest Industry Brand Value (measurement)
- Target Industry Quality Leader
- Target Industry Manufacturing Efficiency Leader
Examples of Enterprise or Balanced Scorecard-type KPIs (High-Level):
- Increase Branded flour and bakery goods product
- Corporate Profit Margins will be within top 20% of market leader
- Meet Product Costs targets
- Reduce Employee Turnover 35%
- Reduce Employee Injury Incidence 90%
- Meet Corporate Profit Budget
- Meet Order Fill Rate of 96%
- Reduce Compliance Response Time to 60 minutes
- Meet Production Product Mix Goals of …
- Produce at 90% Scheduled vs. Actual Production
Example of Production KPIs
- Produce to Net Weight Specification
- Reduce Non-branded Production Mix 15%
- Reduce Planned and Nonplanned Down Time 35%
- Reduce Packaging Costs 18%
- Increase Grade A Percentage to 95%
- Meet Net Asset Management Goal
- Run Process to specification
- Operate with Real-Time Electronic Data Collection and Reporting on an hourly basis
- Meet Labor Forecast Accuracy Goal of 95%
Example of Quality KPIs
- Meet HACCP Critical Control Point Measure Targets 100% of time
- Produce to Specification on all Product
- Produce to Quality Standards within each Department Area
- Achieve Real-time Regulatory and Quality Feedback
- Provide Real-Time Microbiological Data Tracking and Feedback
- Provide Real-time Case Lot Tracking
Example of Machine Processing KPIs
- Meet Mixer proficiency targets from supplier
How can I develop trusted and reliable KPIs?
For more information on developing trusted, reliable, and secure operational and business KPIs , contact Dr. Darrel Suderman for a consultation.