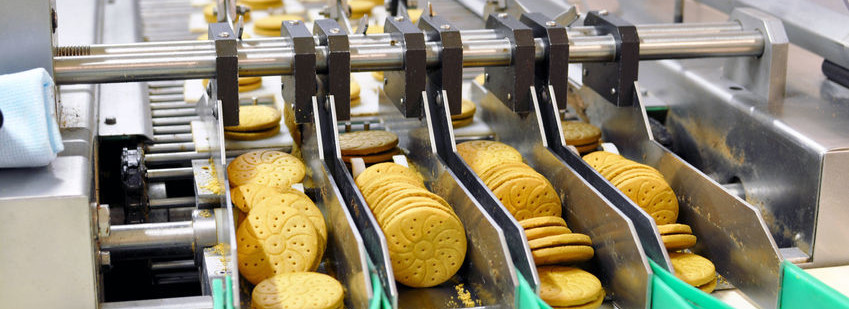
Lights bulbs are a great candidate for a “Run To Failure” maintenance strategy, but not a bakery. So how do you avoid RTF to fail and add value from a predictive/preventive maintenance program?
“Planned Maintenance,” whether it be predictive or preventive, requires you to take actions in advance of a unplanned event. The obvious recipe for disaster is to either have the “wrong” plan, a failure to execute or both. If you are in Run to Failure, then your ability to control and plan your day has been consumed by “unplanned events.” Preventive maintenance and especially predictive maintenance depend strongly on “plan the work and work the plan.” That’s why you need an intervention if you plan on getting out of RTF and the longer you wait, the harder it is.
Some equipment suppliers have started providing equipment based PM’s through the HMI, but you really need a CMMS that collectively manages all the maintenance resources, assets, routines and spare parts. This is almost always an additional expense, but it pays strong dividends if setup correctly and managed with a high level of accountability.
I’ve worked with dozens of CMMS systems and suppliers over the past 38 years and they are not created equal. I have a couple favorites and lots of experience setting up a maintenance department for a bakery, both new and old. We can help you develop the “right” preventive maintenance plan and train your associates to manage the program and execute the tasks.
Do you Run to Failure?
- Do you track how your maintenance resources spend their time and compared “Planned Activities” against “Unplanned Activities”?
- Do you have an asset matrix that reflects “How” each asset fails and what should be the most cost effective way to maintain it?
- Do you have a plant wide work order program that allows all the departments to submit work requisitions and track the approval and completion?
- Do you have a KPI Scorecard that tracks relevant maintenance performance indicators and use it to manage your effectiveness?
- Do you hold weekly “down day” pre-planning and post-review meetings with production and sanitation?
If you answered “No” to these key fundamental maintenance management processes than you might be in RTF or headed there. Don’t wait until too it’s too late or think that this storm will simply blow over.
I’ve been in the business more than 38 years and have worked some the some of the biggest and best companies in the world. We can help you reduce your failure rate and build team effectiveness and would like the chance to assist or support you in your efforts. Ovens, Proofer and Coolers are our specialty areas, along with all forms of preventive and predictive maintenance.
Please contact someone at Brixey Engineering, Inc. if you are looking for additional information, support or training. www.brixey-eng.com